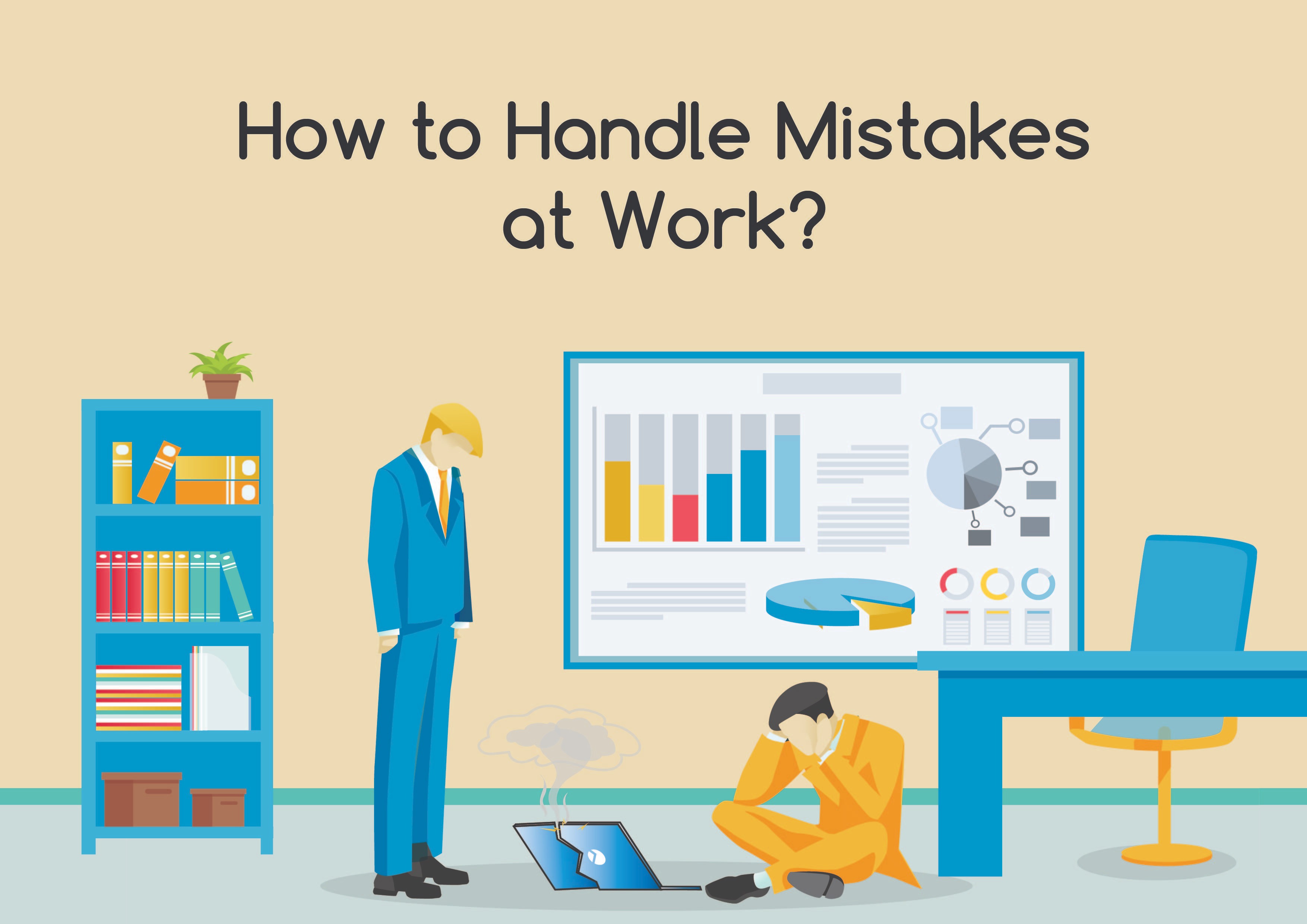
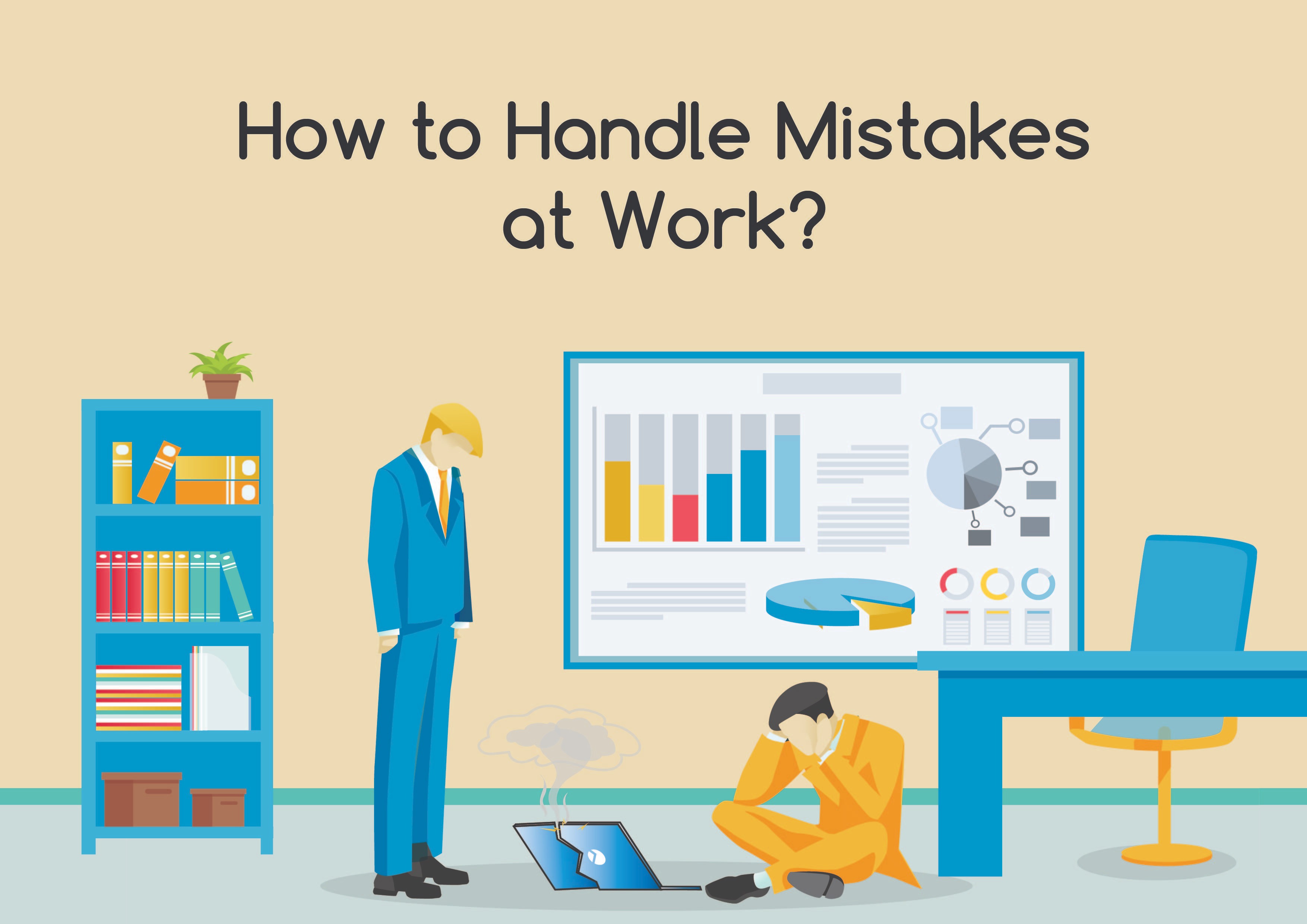
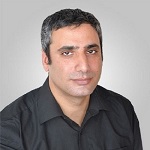
Making mistakes is a reality that nobody can escape.
We may try to fix our mistake by apologizing or by just totally forgetting about it and move on.
But when you make mistakes at work, it can be a different story. The consequences of the mistakes can be much bigger such as losing a potential project, cancellation of existing orders or compromising the health and safety of your colleagues.
I know, that sounds scary. But don’t be sorry yet.
Take a deep breath, let’s talk about it more deeply.
We all make mistakes, we are humans after all.
As they would always say, nobody is perfect.
According to a study conducted by Lappeenranta University of Technology in Finland, human errors or human activity based errors is the top reason of manufacturing mistakes. These errors include wrong interpretation of information, mistakes in work instructions or drawings, forgetting matters, lack of interests, carelessness, and not skilled workforce.
Despite this, there is always a way to avoid the mistakes completely.
Yet, there is also the option to do nothing at all.
How to avoid making mistakes? Prevention is better than cure.
There can be a lot of reasons why mistakes happen. But before it arise, it is best to be prepared so you can avoid it.
1. Ask lot of questions.
First thing is as simple as asking a lot of questions, like a LOOOOOOT of questions.
Asking questions within yourself, with your team, with your suppliers and with your customers can help you learn new things and understand the areas you don’t know about.
But some people would still prefer discovering things on their own or keeping all the questions in their mind, which eventually lead them to being stuck or to making poor decisions.
Asking questions clarifies directions, saves times and resources, and promotes better decision-making. The answers you can get will definitely affect the quality of the decisions you make.
2. Don’t assume – confirm your doubts.
Being resourceful is a good thing, especially when you learn with your own research. But making your own assumptions is another thing.
In the middle of your research on learning new things, you may have some suspicions or doubts. You may catch yourself with these familiar lines: “I think… Maybe… I guess…” - and that should give you an alert.
You can deal with those doubts by confirming things with the right person. When you get the right answers to your questions, it will help you make a clear view and fix your doubts.
3. Identify the common mistakes and understand how to avoid them.
In your daily grind, you might perform different procedures that require a lot of steps before you can finish and get the final result.
In manufacturing company for example, to produce product, there can be a lot steps to ensure its quality. From receiving the raw materials, cutting, stitching, printing, assembling, labelling and packing, until shipping the final product.
By identifying and understanding the loopholes or areas in the process where mistakes can possibly happen will help you discuss with all the involved parties (such as your team, customers or suppliers), on how to avoid such mistakes, and to come up with solutions in case the errors happen.
4. Communicate effectively.
Language barrier is a common excuse of miscommunication. But as we all know, communication is a two-way street for it be effective.
As discussed in our previous post on Communication Tips to Avoid Manufacturing Issues with Suppliers, we need to keep our language simple and clear, with the intention to express and not to impress. This is very important especially if you are in international business and working with different cultures who have different levels of the English language.
Using visuals such as illustration to explain some important points better will also help in bridging those communication gaps.
5. Understand the process – visit the site to see the actual procedures.
If you work in a manufacturing company, in order to be fully informed how your product is produced, referring to manuals, guides and instructions will help a lot. In addition, if you also go to the actual location where the magic happens, it can be a big difference.
Or if you work in a tech company, going to the research and development area where new apps and tools are developed may help you to understand the service that your company provide.
Going to the site can sometimes be very inconvenient. But visiting the actual location and see the actual process will help you understand the process better.
This can be more costly in terms of time and effort (and sometimes money if you need to travel), but it is definitely worth the hassle if you think about the possible mistakes that you can avoid if you do it.
What to do when mistakes happen? Sorry is not really the solution.
“OMG! I am sorry. It’s all my fault. Please forgive me. Please. Please… Please… ” *cries with heavy breathing*
Well, it maybe not an actual scene. But what I am trying to say is, don’t be too dramatic.
Mistakes are normal. It is acceptable as it is part of growth and innovation. What is not acceptable is when you don’t take actions to fix the issue.
Below are some of the practical tips on what to do when dealing with product defects or mistakes in manufacturing.
1. Report immediately.
Reporting the issue right after you identify it can make the process of solving the problem much faster and avoid bigger damage.
Not reporting and keeping it in yourself is like hiding something which can greatly affect the trust between you and your colleague. Worst thing to happen is if you customer would find out about the problem without you informing them.
Most business partners work with trust. It is built over a period of time, but it can also be broken in a split of second with one lie. So it is best to take care of that trust at all times.
2. Leaders empower the Staff.
When someone from the team comes to report an issue, team leaders or senior managers should give an encouraging reaction on the staff’s honesty to report the issue. In this way, the team will not be afraid to report, or try to hide when mistakes happen.
Leaders should also not just give solution for team when problems happens. They should train their team as well to be problem-solvers when unexpected situations arise.
3. Make action plan and start to solve the issue.
Once the problem and root-cause are identified, the responsible persons involved should make an action plan together and start to solve the issue.
This is the most important part when errors happen. As mentioned, being sorry is okay but “sorry” is just an emotion. But taking the action to fix the problem is the solution.
4. Take responsibility and keep your customers updated.
In such cases that your customers are affected because of the mistakes, it is best to keep them informed and updated.
“What??? You are a long-term vendor! How could this mistake happen?!?!! RAWWWRRR!!!”
Well, maybe not.
But yes, maybe your customer will get angry and disappointed. It is normal, that’s something that you have to remember, they are also humans and they have emotions.
At the same time, your customers also know that mistakes can happen, and they for sure will understand after they get relaxed.
So allow them to take it out, and keep them assured that everything is being taken care of by telling them the actions that you will take to fix the problem.
5. Improve the process.
Fixing the problem is not the end of the solution.
To avoid the same situation to happen, you have to check which areas in your process need some points to improve.
This can be from the automation of your inventory system, technical training on your workforce, restructuring your workflow, maintenance of machine and equipment, practicing daily team stand meeting, sourcing of new suppliers, etc.
Remember that everyone makes mistakes, you are not an exemption. You might also feel horrible when mistakes happen. But the good news is, you can avoid it and you can fix it with the right mindset and action steps.
Most importantly, learn from your mistakes and don’t let yourself have that negative self-talk. The mistakes you make at work will not ruin your career, but how you react to them can.